High Temperature Additive System Design
Master's Research (Boston University)
Design a system for patterning high-temperature metals and functional oxides.
Design a system for patterning high-temperature metals and functional oxides.
Overview
System designed for additive patterning of high-temperature materials in a way that can use process parameters
to change functional behavior through relationships between cooling rate and crystal structure or in-situ
reactions, including metals and functional oxides. The method utilizes a "Direct Ink Writing" method, where
fluid is driven out of the nozzle with high pressure.
Induction Heated
Single-piece nozzle for use at temperatures up to 800°C
Silicon Carbide Coated Graphite Nozzle
Air-driven and cooled
Single-piece nozzle for use at temperatures up to 800°C
Single-piece nozzle for use at temperatures up to 800°C
Silicon Carbide Coated Graphite Nozzle
Air-driven and cooled
Single-piece nozzle for use at temperatures up to 800°C
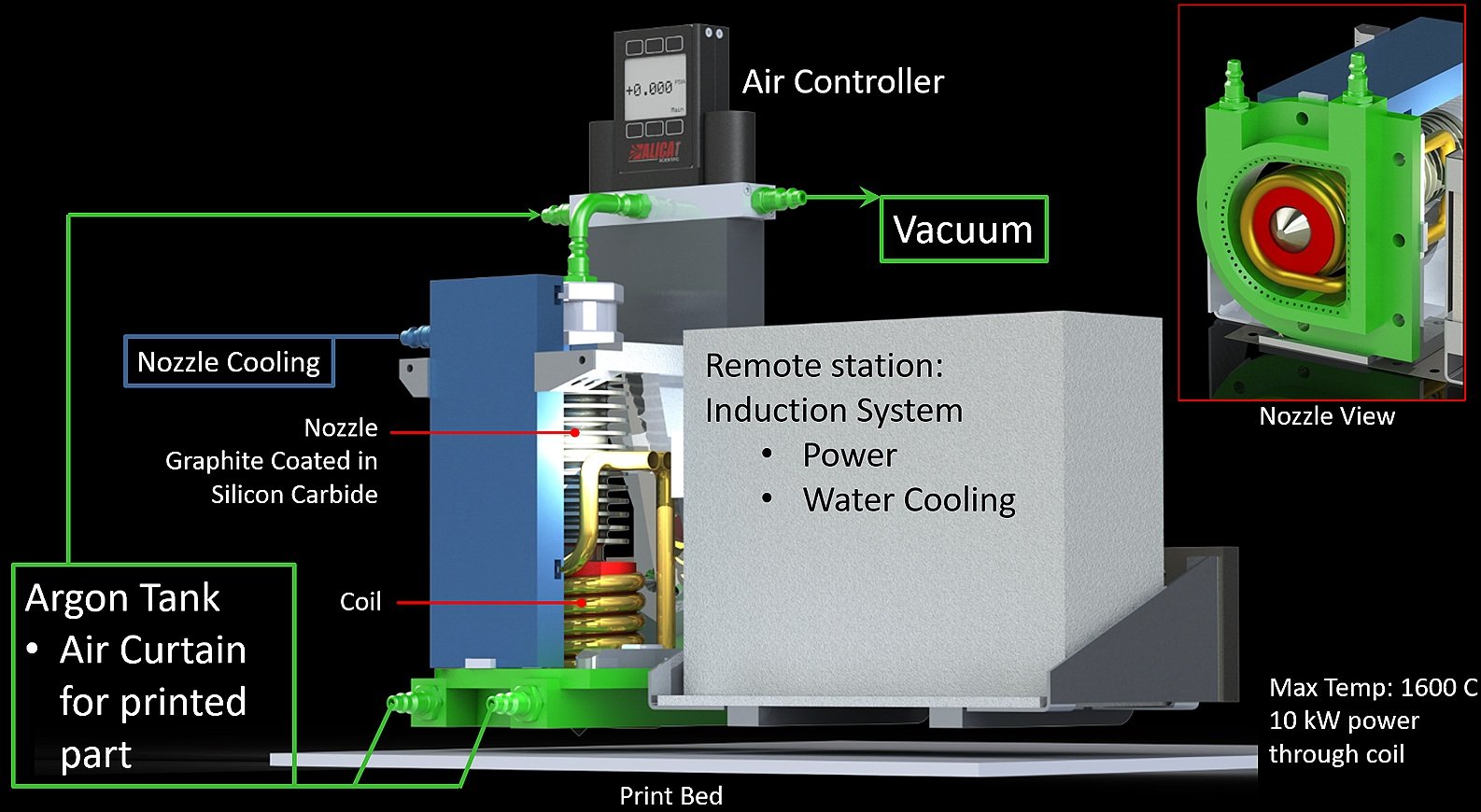
Induction Heating
Induction Heating provides a more direct heating method for very high temperatures in atmospheric conditions.
This provides a more efficient and responsive heating control when working in open air environemnts with limited space, allowing for a smaller more compact nozzle head.
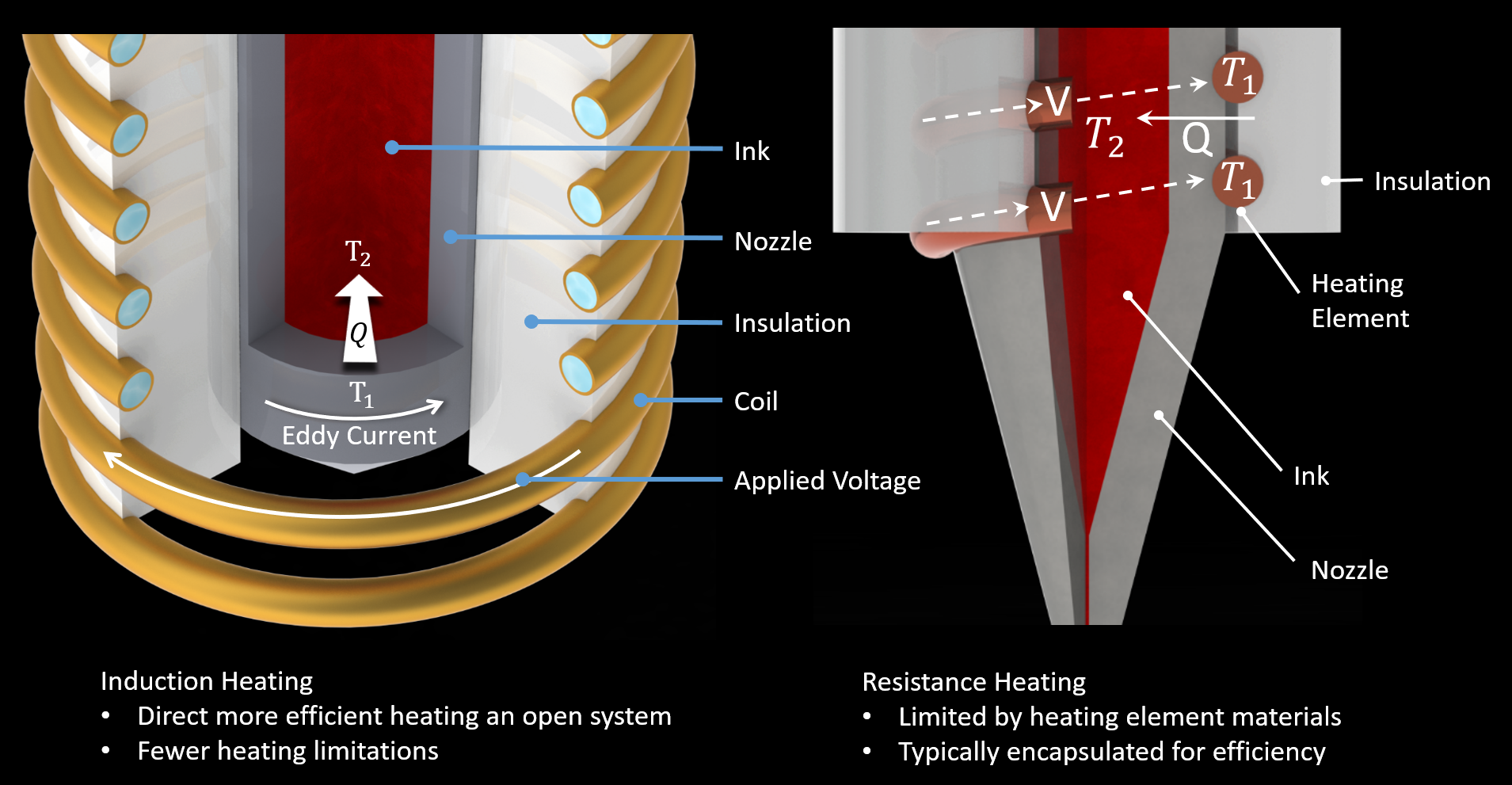
Nozzle Design
The nozzle was designed as a single piece with an air-cooled heat exchanger to lower the temperature at the connection point.
A MATLAB PDE solver was used to explore the geometric parameters of the nozzle. Many assumptions were made to simplify the model,
but these were inaccurate to actual operation and later re-evaluated when the prototype was produced.
2D Axisymmetric model with forced convection cooling
Parameter space sweep included number of fins, length of fins, and thickness of fins.
Temperature was evaluated at the connection point
Original prototypes were tested with tungsten, as shown.
Parameter space sweep included number of fins, length of fins, and thickness of fins.
Temperature was evaluated at the connection point
Original prototypes were tested with tungsten, as shown.
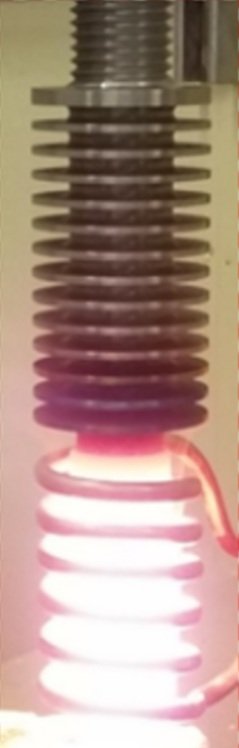
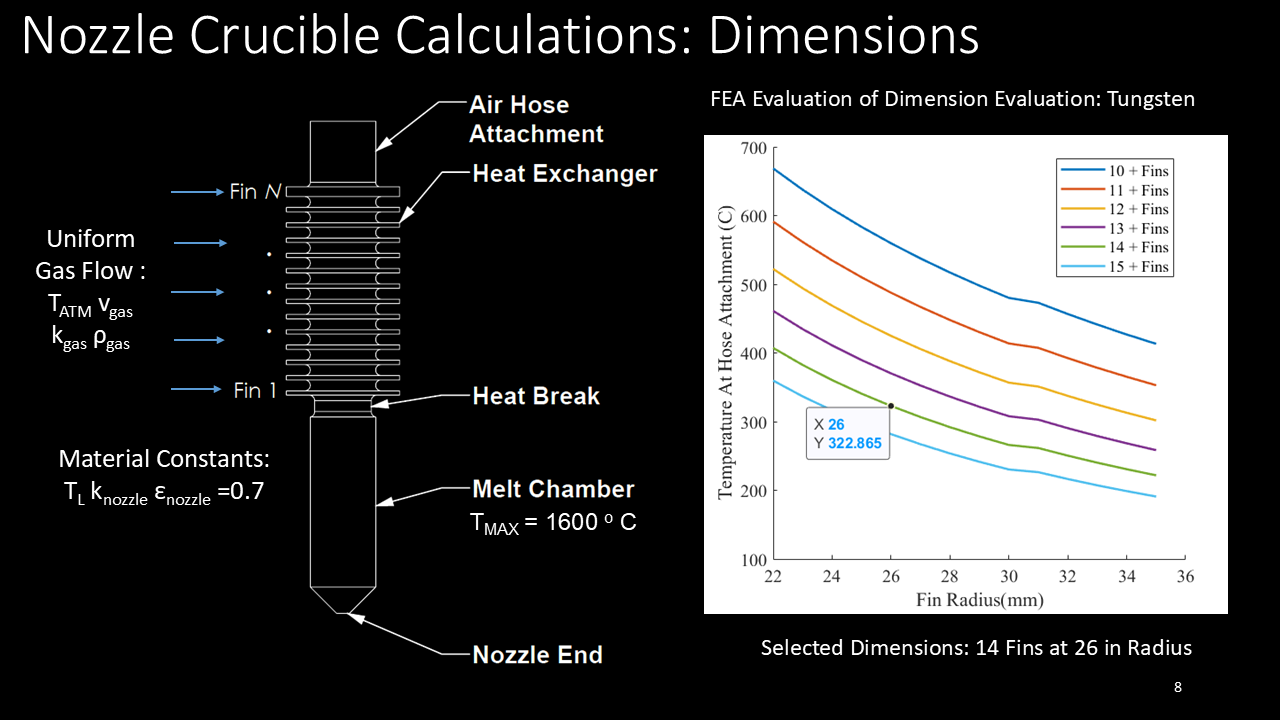
Operational Parameter Evaluation
Based on former work from my advisor, a simulation was developed to evaluate the solidification rate of
molten materials over different process parameters.
Parameters: Print speed, print temperature, cooling temperature
Substrate material can be selected to evaluate re-melting or fusion of layers
Fortran custom numerical estimation code with Central Differencing for general temperature profile evaluation, with Left Differencing used to account for movement of the hot zone (nozzle)
Ability to differentiate phase change with property evaluation per cell (heat capacity and thermal conductivity)
Substrate material can be selected to evaluate re-melting or fusion of layers
Fortran custom numerical estimation code with Central Differencing for general temperature profile evaluation, with Left Differencing used to account for movement of the hot zone (nozzle)
Ability to differentiate phase change with property evaluation per cell (heat capacity and thermal conductivity)
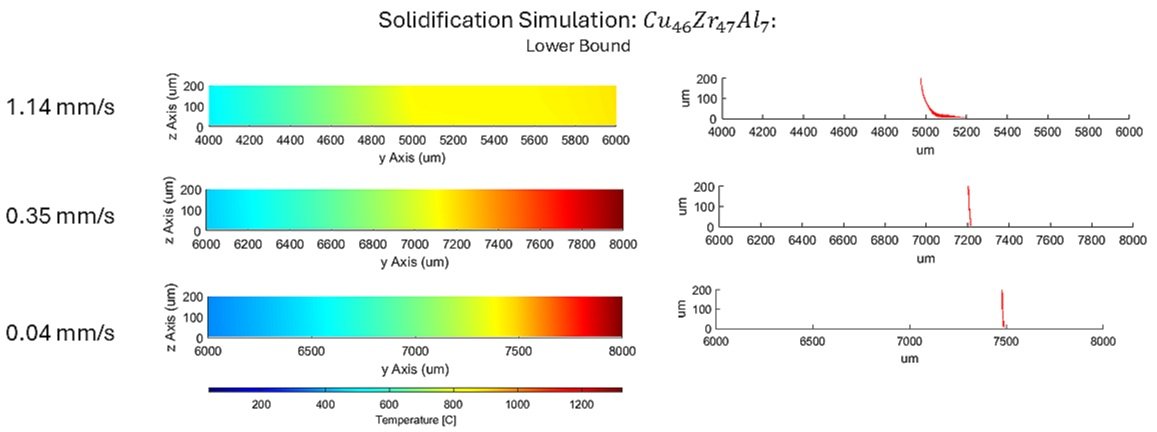
Build Images
System components were completely machined in house, with the induction system sourced from a vendor.
Full system attached to lab's Cartesian Gantry System
Hot end assembly
Infrared Thermocouple
Hot end assembly
Infrared Thermocouple